Aumentar la productividad con los últimos estándares de fábrica conectada
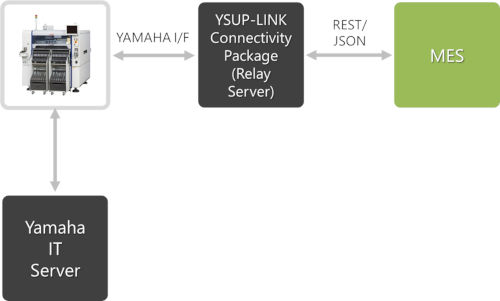
Las tecnologÃas de la Industria 4.0 no sólo tienden puentes entre los equipos de fabricación y la gestión empresarial, sino que están permitiendo nuevas herramientas de gestión de fábricas que ayudan a los equipos de producción a mantener los procesos en marcha de forma fluida y eficiente.
El Internet Industrial de las Cosas (IIoT), como habilitador clave de la Industria 4.0, está transformando la forma en que se manejan los datos tanto en el ámbito de las tecnologÃas operativas (OT) como en el de las tecnologÃas de la información (IT).
Está impulsando la aparición de nuevas herramientas que pueden mejorar la planificación de alto nivel, asà como el mantenimiento y la optimización en la planta de producción.
Los estándares mejoran la conectividad
La IIoT incorpora potentes protocolos estandarizados de comunicación entre máquinas. En la fabricación de productos electrónicos de montaje superficial, estos protocolos proporcionan ahora una base para la comunicación significativa entre los equipos automatizados en lÃnea y el software de nivel empresarial, como el sistema de ejecución de fabricación (MES) y la planificación de recursos empresariales (ERP). Se trata de una mejora de gran acogida porque, históricamente, la falta de normas y los gastos y el esfuerzo de desarrollo de software necesarios para mantener la compatibilidad han frenado las perspectivas de comunicación sofisticada entre los distintos tipos de equipos y sistemas.
Otra mejora es que los cambios en la forma en que las máquinas comparten datos también permiten ahora a los proveedores de equipos SMT mejorar las herramientas de software a disposición de los equipos de producción que trabajan en la fábrica. A pesar de la tendencia general a una mayor automatización y a periodos más largos de producción sin supervisión, la complejidad de los procesos y equipos SMT -que requieren una atención frecuente para su mantenimiento y optimización- implica que la potenciación de estos equipos sigue siendo importante.
Conectar los ámbitos de OT e IT
Como uno de los principios definitorios de la Industria 4.0, la conexión de los equipos de OT de una organización con sus sistemas de TI tiene como objetivo crear un vÃnculo perfecto entre los equipos de la fábrica y las aplicaciones que dirigen el negocio. Permite que el software empresarial como el MES automatice el control de las actividades de fabricación, mientras que los datos de los equipos de la fábrica también impulsan aplicaciones analÃticas que informan la planificación empresarial y proporcionan los conocimientos necesarios para la mejora continua.
Las tecnologÃas IIoT incorporan ahora protocolos y API estandarizados, como JSON (JavaScript Object Notation) y REST (REpresentational State Transfer), que permiten la comunicación entre los equipos de la fábrica y las aplicaciones informáticas. Sin estas plataformas estandarizadas, la compatibilidad entre equipos y aplicaciones dista mucho de ser "plug-and-play", y requiere una colaboración costosa y laboriosa entre los equipos de desarrollo de software de las distintas partes.
Gracias a estos protocolos, los equipos y las aplicaciones pueden compartir datos a través de una interfaz de comunicación relativamente sencilla. El fabricante del equipo puede crear y mantener esta interfaz sin necesidad de personalizarla para permitir la comunicación con aplicaciones informáticas individuales especÃficas. Un ejemplo es YSUP-LINK, que forma parte del sistema de apoyo a la producción YSUP de Yamaha. Utiliza REST para permitir que equipos de montaje superficial como una impresora automatizada YSP10 y las últimas montadoras YRM20 de una lÃnea de producción se conecten a varias MES de terceros u otras aplicaciones de Industria 4.0. También se encarga de controlar y recopilar información de los equipos de la lÃnea de producción y se conecta al almacenamiento inteligente de componentes, además de admitir la posibilidad de conectarse con equipos y software de terceros en el futuro.
Figura 1. YSUP-LINK aprovecha los protocolos estándar de la industria para conectar la automatización de la fábrica con el software de la empresa.
En efecto, proporciona un paquete de conectividad que permite a los equipos de la fábrica enviar información de estado al MES, lo que permite a éste supervisar y gestionar automáticamente las actividades de fabricación (figura 2).
Figura 2. YSUP-LINK proporciona la conectividad necesaria para que un MES gestione la fabricación automáticamente.
Múltiples instancias de máquinas como la YRM20 pueden conectarse simultáneamente a este entorno, lo que permite a YSUP-LINK enviar informes al MES, como actualizaciones de estado en directo sobre los materiales que se están utilizando en cada máquina, o informes de reposición cuando se cambian las bobinas.
También es compatible con la interfaz SECS/GEM heredada, que facilita la comunicación entre el nuevo software y equipos como el entorno de procesamiento back-end de semiconductores, que utiliza protocolos establecidos.
Por otro lado, de cara al futuro, está preparada para el próximo protocolo de intercambio de fábrica conectada IPC-CFX (IPC-2591), cuyo objetivo es establecer una norma única para todos los aspectos de la gestión de datos y comunicaciones en las fábricas digitales.
Enriquecimiento de las comunicaciones OT
El sistema de apoyo a la producción de Yamaha también incluye un sistema de información de materiales, YSUP-MI, que centraliza la gestión de la información de materiales y la pone a disposición de las herramientas de software de la fábrica para actividades como la supervisión de lÃneas y la verificación/navegación de configuraciones. Esto ofrece ventajas a los equipos de producción, como una respuesta acelerada a las solicitudes de información sobre bobinas por parte de los operarios, y también permite una ejecución más rápida de las copias de seguridad de los datos.
La gestión se centraliza gracias a la sincronización en tiempo real entre el sistema de información de materiales y los sistemas informáticos de la empresa
En la fábrica, es fundamental garantizar que los equipos de operaciones se mantengan informados del estado de los equipos y de la producción, y que estén facultados para tomar medidas correctivas cuando sea necesario.
Aprovechando el servidor de transmisión, un operario que trabaje en una máquina puede enviar una instrucción a todas las demás máquinas de la lÃnea simultáneamente. Todas las máquinas pueden compartir operaciones básicas como el control de marcha y el cambio de programa, mientras que las últimas generaciones de equipos YRM permiten intercambios como la carga de placas, la visualización de pantallas y el estado de máquinas y placas.
Además, el software YSUP proporciona un panel de control (dashboard) en directo que ofrece análisis mejorados para ayudar a la optimización en tiempo real y a la resolución de problemas. Esta herramienta incluye funciones analÃticas como el análisis de los resultados de impresión, el análisis de la alineación de la colocación, el soporte del proceso de visión, la incorporación de costes de pérdidas y la generación de informes mejorados que respaldan las actividades de mantenimiento y ayudan a mejorar la productividad.
También dispone de análisis de recogida de componentes, que ayuda a encontrar y remediar las causas de los defectos comunes de montaje. Este sistema ya ha proporcionado notables resultados a algunos clientes. Al visualizar simultáneamente las tasas de errores de recogida por alimentador y por cabezal, el cuadro de mandos ayuda al equipo a localizar un problema de recogida en un fallo con la cinta de empalme que podrÃa haber tardado unas 6 horas en identificarse con las herramientas tradicionales. La figura 3 compara los procesos de diagnóstico de ambos enfoques y muestra cómo el panel de control redujo el tiempo de resolución del problema a unos 40 minutos..
Figura 3. Resolución de problemas basada en los registros de errores tradicionales (izquierda) y en el nuevo análisis de Dashboard (derecha).
De forma similar, otro cliente ha aprovechado la información del panel de control para reducir los errores mensuales de recogida en más de 100.000, lo que supone un ahorro potencial de entre 12.000 y 120.000 dólares al año en pérdidas de componentes.
Â
Conclusión
Las tecnologÃas IIoT están permitiendo una sofisticada comunicación plug-and-play entre equipos de montaje en superficie, herramientas de software de fábrica y TI de nivel empresarial. Por un lado, esto proporciona el tan esperado puente entre los dominios de TI y OT de las empresas, para automatizar la gestión de la producción y aumentar la eficiencia. Por otro, sienta las bases de herramientas de software de fábrica mejoradas que aumentan la visibilidad para los operarios de los equipos y aceleran la resolución de problemas y la optimización de procesos para maximizar la productividad.
Articulos Electrónica Relacionados
- Plataforma Cognex Edge Intelli... Cognex Corporation presenta Cognex Edge Intelligence (EI). La plataforma ofrece una supervisión del rendimiento de la lectura de códigos de barras y una gestión...
- Controlador industrial PLCnext RS Components (RS), marca comercial de Electrocomponents plc ha presentado el primer controlador lógico programable (PLC) basado en la plataforma de cont...
- APIs Cloud para pasarelas IoT El camino para conectar y poner en marcha soluciones en la nube pasa a través de la estandarización de APIs. La orquestación de red de sens...
- Soluciones de ON Semiconductor... Farnell comercializa una amplia gama de productos de ON Semiconductor destinadas al nuevo marco desarrollado por ON Semiconductor y Avnet para ayudar a los subc...
- Sistema de control distribuido... ABB Ability™ System 800xA 6.1.1 mejora la colaboración con una serie de funciones nuevas que incluyen una puesta en marcha simplificada y más rápida para proyec...
- Habilitar la fábrica del futur... A medida que la demanda de fabricación más inteligente, segura y eficiente continúa aumentando, la automatización avanzada está respondiendo al llamado, transfo...
- PC industrial Aaeon BOXER 6404... El PC BOXER-6404U con slot SIM de Aaeon es equipo de tamaño muy compacto y gran capacidad de conexión que será una potente pasarela de dato...
- Festo Motion Terminal VTEM con... Festo Motion Terminal VTEM catapulta la neumática a la era de la Industria 4.0, con Apps que le permiten sustituir a más de 50 componentes individ...
- White paper gratuito de Frost ... La llegada de tecnologÃas TIC avanzadas al sector de la fabricación tradicional está creando un nuevo ecosistema de fábricas denominado "Smart Factory". Este wh...
- Controlador de seguridad SICK ... Un controlador de seguridad es el componente central de todas las aplicaciones de seguridad. Es el encargado de evaluar la información de los sensores e interru...
- Controlador de movimiento XMC ... Vector Motor Control (VMC) presenta el nuevo motion controller XMC de LS Electric, un equipo capaz de gestionar hasta 32 ejes a alta velocidad con comunicación ...
- Principales retos de la Indust... La adopción de la Industria 4.0 ofrece muchas ventajas, pero también presenta muchos retos cuando las empresas intentan superar los obstáculos técnicos, organiz...